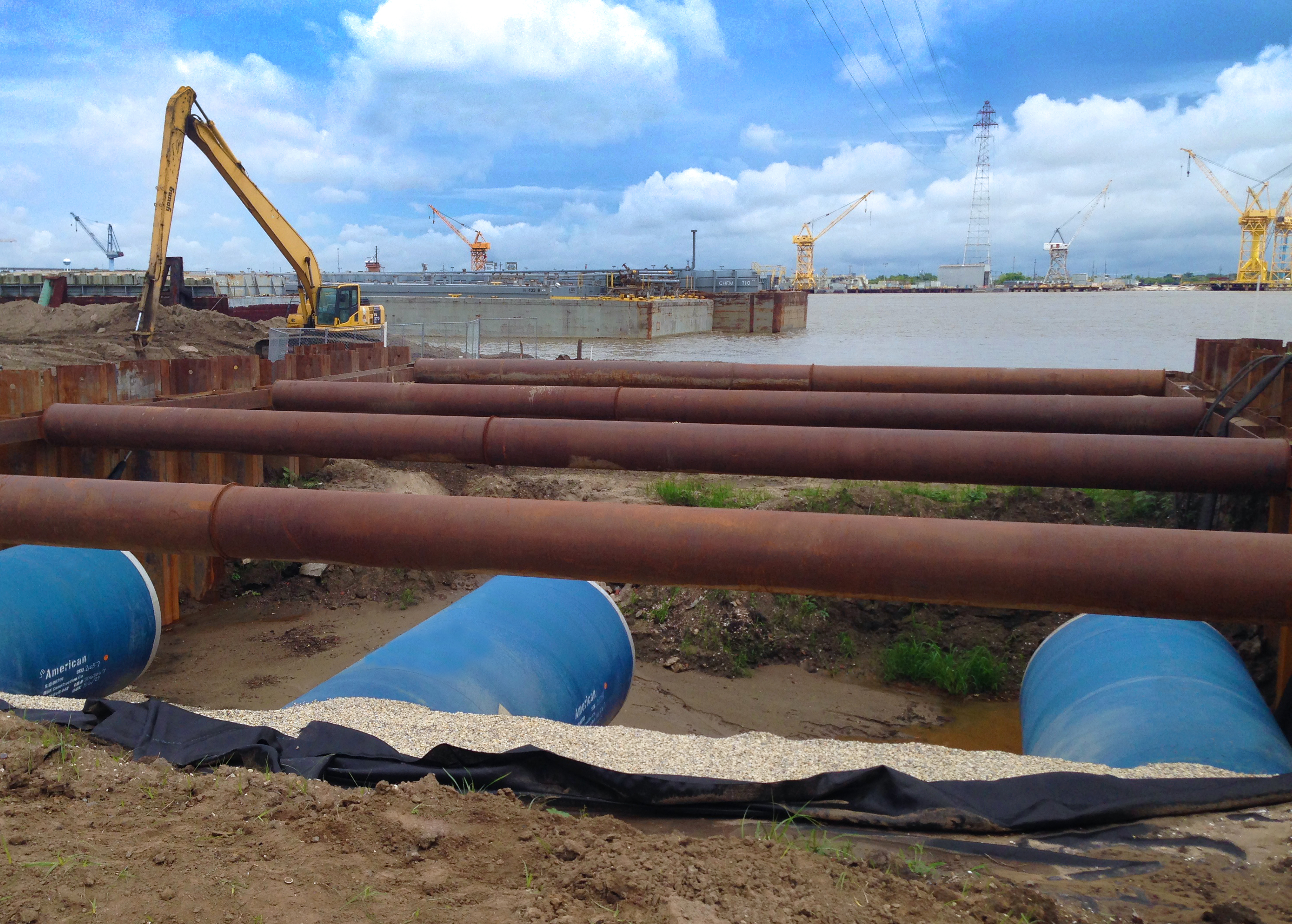
This article also appeared in American City & County. Read the article here.
If you think Hurricane Katrina was the first time New Orleans suffered major flood damage, think again. Flooding has been as much a part of New Orleans’ 300-year history as jazz, jambalaya and French Quarter juke joints.
One of the city’s worst floods ever came in the mid-1990s, and that led to the creation of the Southeast Louisiana Urban Flood Risk Reduction Project (SELA). The main objective for SELA is to reduce flooding in three parishes — Orleans, Jefferson and St. Tammany. Funding issues stymied SELA’s initial progress, but federal money began pouring in after a Katrina-related levee break flooded 80 percent of New Orleans in 2005.
According to the U.S. Army Corps of Engineers’ website, SELA’s overall objective in Orleans and Jefferson parishes is to modify and improve drainage and pump excess water from flood-prone areas into the Mississippi River. Those waters currently drain into Lake Pontchartrain. Plans for St. Tammany Parish include channel enlargements, bridge replacements, detention ponds, levees and elevation of flood-prone structures. A substantial amount of this work has been completed in Jefferson and Orleans parishes, but work has yet to begin on the St. Tammany Parish projects, according to the Corps’ website.
A major element in SELA’s work is the need for huge pumping capacity, and AMERICAN’s spiral-welded steel pipe is playing a major role in that scenario. Begun several years ago, SELA’s $100 million-plus Harahan Pump to River project has relied on AMERICAN piping along the way. B&K Construction Co., LLC, of Mandeville, Louisiana, currently is executing a $24.3 million Harahan Pump to River contract that involves the installation of more than 6,000 feet of AMERICAN 84-inch-diameter spiral-welded steel pipe.
The piping consists of three different lines being installed underground along Powerline Drive from Jefferson Highway to River Road Drive. From there, the lines continue up and over the levee to the Mississippi River. Pumping capacity is 1,200 cubic feet per second. B&K Construction started this phase of the project in March 2013 and is slated to finish it in early 2016.
In addition to providing all discharge piping for this project, AMERICAN also is supplying fabricated discharge cones, according to Bo Markovic, project manager with B&K Construction. “Their (AMERICAN) product is one of the best our field personnel have dealt with in recent years,” Markovic says. “The pipe is being delivered on flatbed trucks, and it’s cradled for support and tied down with nylon straps to protect the exterior coating. Interior cribbing is used to keep the pipe diameter true to its dimensions.
“Their (AMERICAN) product is one of the best our field personnel have dealt with in recent years.”
“The quality control inspectors on the project have not had any issues with the pipe coating, handling, length, roundness or thickness of the interior mortar lining,” Markovic says. “Comments from welders and operators while handling and installing the pipe often include remarks on how well the pipe fits together and how easy it is to handle.”
Markovic notes that AMERICAN’s service on this contract has been as steady as its spiral-welded steel pipe. “We’ve dealt with AMERICAN’s sales representatives and production and shipping personnel throughout the length of this project,” he says. “Their estimate for the cost proposal was easy to follow, well thought-out and concise. Upon the award of the project and before production of the pipe begun, we set up a meeting with their sales engineers and the production managers from AMERICAN. They were well-prepared and conducted themselves in a professional manner.
“The pipe production was on time. Communication between the production facility and the B&K field staff was constant and flowed without issues. AMERICAN’s sales representatives continue to make frequent visits to the job site and follow up with all requests.”
With service like that, B&K Construction can devote more focus to the real-world problems of building such a project — problems that are easier to address without inferior piping and service issues. “The biggest challenge on any underground project streams from the possibility of encountering unforeseen structures while excavating,” Markovic says. “The challenge is approached with a calm mind and input from management and the design team. A solution is proposed and the structure is removed.”
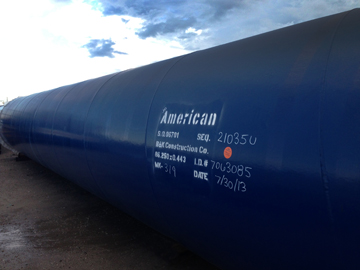